Outlook
Partnership opportunities
COP28
Partnership opportunities
Congress 2023
Powering Sustainable Growth
Join us in Bali for the 2023 World Âé¶¹ÊÓÆµ Congress taking place on 31 October – 2 November.
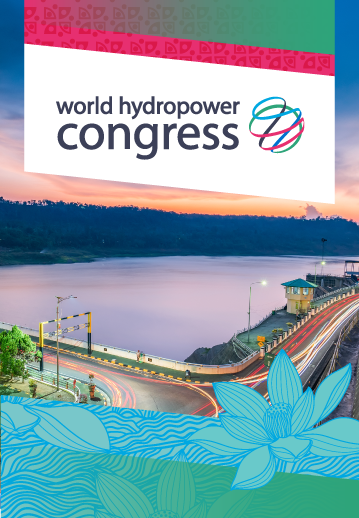
Who we are
Our mission
Our mission is to advance sustainable hydropower
About Âé¶¹ÊÓÆµ
We are a non-profit membership organisation
Our members
View our directory of organisations operating in over 120 countries
Our team
Âé¶¹ÊÓÆµ's Central Office manages our work programmes
Our board
Âé¶¹ÊÓÆµ's Board governs the association on behalf of members
Our story
The voice of sustainable hydropower for a quarter of a century
What we do
Communications
Our mission is to advance sustainable hydropower
Policy and Insights
We are a non-profit membership organisation
Events
View our directory of organisations operating in over 120 countries
Membership
Âé¶¹ÊÓÆµ's Central Office manages our work programmes
Water management
Âé¶¹ÊÓÆµ's Board governs the association on behalf of members
People
The voice of sustainable hydropower for a quarter of a century
Technology
Our mission is to advance sustainable hydropower
Regional profiles
Africa
Our mission is to advance sustainable hydropower
East Asia and Pacific
We are a non-profit membership organisation
Europe
View our directory of organisations operating in over 120 countries
North and Central America
Âé¶¹ÊÓÆµ's Central Office manages our work programmes
South America
Âé¶¹ÊÓÆµ's Board governs the association on behalf of members
South and Central Asia
The voice of sustainable hydropower for a quarter of a century
Pumped Storage
Pumped storage hydropower toolkit
Policy frameworks for pumped storage hydropower development
Enabling new pumped storage hydropower
A guidance note for key decision makers to de-risk pumped storage investments
International Forum on Pumped Storage Âé¶¹ÊÓÆµ
Find out how you can participate in the Forum in Paris on 9-10 Sept 2025
Tracking tool
Locations and vital statistics for existing and planned pumped storage projects
Facts about pumped storage hydropower
Find out more about the benefits of pumped storage
Global Alliance for Pumped Storage
Intergovernmental leadership group dedicated to promoting, scaling, and optimising PSH worldwide
Resource hub
Publications
Download our public reports
World Âé¶¹ÊÓÆµ Outlook
Sector insights and statistics
Factsheets
Learn more about hydropower
Facts about hydropower
Get the full picture
Âé¶¹ÊÓÆµ around the world
Explore regions and countries
Innovations hub
Explore case studies
Videos
Watch our latest videos and webinars
Sediment Management Hub
Knowledge resource for strategies and case studies