Better Hydro: Asset reliability and efficiency at Nam Lik 1-2, Laos
This project features in our 'Better hydro: Compendium of case studies 2017', available for download here.
Key project features
Project stage: operation
Developer/operator: Nam Lik Power Company (NLPC)
Capacity: 100 MW
Annual generation: 485 GWh
Purpose: power generation
Rigorous monitoring of equipment performance, together with an effective maintenance routine, has enabled the Nam Lik 1-2 project to exceed the terms of its power purchase agreement and generation target every year since commissioning. The project demonstrates excellence in asset reliability and maintenance.
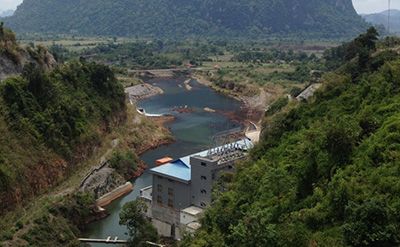
Nam Lik 1-2 is located on the main stream of the Nam Lik river, to the north-west of the capital of Laos, Vientiane. The dam is located in the district of Mueng Fueng, and the river flows downstream through the Hin Heup district, where it joins the Nam Xong to form the Nam Ngum. This flows into the Mekong river, downstream of Venetiane.
The project has an installed capacity of 100 MW, and is equipped with two 50 MW Francis turbines, which are coupled with 58 MVA generators. The turbines and generators were manufactured by the Hangzhou Resource Power Equipment Company, and have a predicted lifespan of 25 years. The main structures of the project are: a reinforced concrete-faced rockfill dam; spillway; flood release tunnel; headrace tunnel; powerhouse; switchyard (located on the top of the powerhouse); and a saddle dam.
The Nam Lik 1-2 project demonstrates excellence in asset reliability and maintenance."
The project is fully owned by the Nam Lik Power Company (NLPC), which is a joint venture between the China International Water and Electric Corporation (CWE) and Électricité du Laos (EDL). NLPC does not own or operate any other project. CWE owns a 90 per cent share of NLPC and EDL owns 10 per cent. CWE is a subsidiary of the China Three Gorges Corporation, and manages CTG’s overseas investments.
NLPC and the Lao Committee for Planning and Investment agreed in 2006 to a 25-year build-own-operate-transfer contract. The project was licensed in 2007 and commissioned in July 2010.
Rigorous monitoring of equipment performance, combined with an effective maintenance routine, has enabled the project to exceed the terms of its power purchase agreement and its generation target every year since commissioning.
NLPC undertakes routine monitoring of the condition, availability and reliability of the project assets using automated and manual methods. This approach has helped the company to regularly identify many minor, and some major, asset maintenance and management issues. The company uses a range of operating manuals, procedures and guidelines. Activities revolve around a monthly production meeting where engineers review asset maintenance and safety issues from the previous month and plan the following month’s maintenance.
Automated measurements support routine monitoring
NLPC undertakes routine monitoring of asset condition using automated and manual methods. Because the project is relatively new, it is equipped with automated asset monitoring and error reporting systems. Every two hours, engineers walk around the plant carrying out routine checks on equipment and recording performance data. Each month, the maintenance department analyses data recorded by the manual inspections and the automated monitoring, and compares performance with the manufacturer’s guidance. This routine monitoring of all equipment allows NLPC to identify any emerging risks.
In 2012, routine monitoring highlighted overspeed in one of the turbines. This prompted a complete overhaul of the turbine, which would normally not have occurred until planned maintenance in 2017. When an issue is spotted, this triggers a physical investigation and full technical review by NLPC engineers. Engineers also compile incident reports following unexpected events that affect generation, such as a lightning strike in March 2015 and a grid failure in May 2014. They then use this information to prepare for similar events in the future.
Manuals and a monthly process systematise routine monitoring
NLPC uses a range of operating manuals, procedures and guidelines for routine monitoring and maintenance requirements of the operating facility. Two comprehensive manuals set out the 'operation and maintenance procedures' and the 'overhaul procedures', to guide operation and maintenance activities. The manuals cover generating equipment, speed control systems, transformers, distribution equipment, diesel generators, computer monitoring, communication systems, water supply systems, compressed air systems and the spillway gates. They also include procedures to follow when monitoring identifies an emerging risk.
Each month, NLPC holds a production meeting to review the asset maintenance and safety issues of the previous month, and to plan the following month’s maintenance. The monthly plan allocates tasks and daily activities to individual staff members. NLPC reports to CWE on a monthly basis with a summary of the monitoring results for generation, maintenance and safety.
Asset categorisation enables prioritisation of maintenance
To manage longer term asset replacement, NLPC classifies equipment into three different categories, according to the required frequency of maintenance and replacement. Category A equipment is the responsibility of the operation group and requires replacement every six to eight years. Category B is also the responsibility of the operation group and requires replacement every three to four years. Category C equipment is the responsibility of the maintenance group and requires replacement annually. NLPC has scheduled the first full overhaul of Category A equipment for 2017, and completed the second category B round in 2016.
NLPC classifies equipment into three different categories, according to the required frequency of maintenance and replacement."
Pre-emptive upgrades ensure optimal condition
Engineers measure the exact level of wear and tear to equipment in their routine monitoring, and determine the optimal time for replacement. NLPC replaces most mechanical assets based on the performance of the equipment rather than its predicted lifespan.
The company also plans to implement efficiency improvements as new technology develops, rather than through a planned long-term programme of upgrades.
There is, however, a long-term programme for electrical assets, requiring replacement and upgrading every seven to eight years, regardless of condition. This is because the engineers believe that technology will improve sufficiently to justify replacement on financial grounds.
Proactive investigation helps identify opportunities for new technology
NLPC’s production team is tasked with investigating areas for improvement in reliability and efficiency, using a number of channels to learn about new technology or research. CWE and CTG send regular updates regarding technological innovations and Chinese regulations on asset performance. The parent companies often send in-house experts to review and advise on emerging issues, such as a review and redesign of the hydrological monitoring system. NLPC employees also have the opportunity to attend CWE and CTG training courses on maintenance.
Each new investment must be justified on financial grounds. Examples of proposals advanced and implemented by the production team include improvements to the back-up power system, and an enhanced telecommunications system to facilitate better communication internally and with local authorities during bad weather.
This case study is based on an official assessment of Nam Lik 1-2 using the operation stage tool of the . The assessment was carried out in 2015, with an on-site assessment held in April 2015.
This case study featured in 'Better hydro: Compendium of Case Studies 2017'. You can browse and download the full publication here.